Production/
Aménagement d'une usine
L’aménagement d’une usine est l’un des éléments ayant le plus d’influence sur la productivité et l’efficacité des opérations d’une entreprise manufacturière. Par conséquent, il importe d’agencer de la façon la plus optimale possible les différents équipements, postes de travail et zones d’entreposage.
Démarche suggérée pour planifier ou revoir l’aménagement d’une usine
- Préparer un plan à l’échelle du nouveau bâtiment (voir l’exemple de plan d’usine).
- Calculer l’espace requis par les différents équipements et postes de travail actuels (et futurs si on prévoit un accroissement de la capacité de production) ainsi que pour l’entreposage des matières premières et produits finis.
- Déterminer l’ensemble des contraintes. Ces contraintes peuvent être liées :
- au bâtiment (portes, fenêtres, colonnes, etc.);
- aux équipements (dimensions des machines et des équipements, espace pour la circulation, dimensions des étagères pour l’entreposage, équipements de ventilation, ponts roulants et compresseurs s’il y a lieu, etc.).
- Travailler sur le plan à l’échelle en déplaçant les différents postes de travail, équipements et étagères d’entreposage de manière à réduire les distances entre les postes de travail consécutifs et à respecter le flux de production en visant un flux continu. Il faut éviter les flux croisés tel qu’il est illustré dans les types d’aménagement présentés. Cette étape peut être réalisée autant sur papier qu’à l’aide d’un logiciel de dessin, p. ex. AutoCaD.
- Valider et bonifier le plan avec les employés par l’intermédiaire d’un comité formé d’employés expérimentés. Idéalement, les employés devraient aussi participer aux étapes :
- 2 (calcul de l’espace requis);
- 3 (détermination des contraintes);
- 4 (travail sur le plan à l’échelle).
Il s’agit généralement d’un processus itératif; il est rare qu’une première version du plan soit retenue sans modification.
- Une fois le plan validé, réfléchir à l’aménagement et à l’organisation des différents postes de travail avec les employés concernés.
- Procéder à l’aménagement physique de l’usine.
- Deux semaines après avoir procédé à l’aménagement physique, évaluer celui-ci avec les employés, prendre note des irritants et problèmes puis apporter les correctifs requis.
Après avoir apporté les correctifs et avoir obtenu un aménagement satisfaisant, appliquer la méthode des 5S aux postes de travail.
Démarche proposée pour l’aménagement physique de l’usine:
- Faire les travaux de construction.
- Planifier les accès, les blocages de rue ou les stationnements et gérer la localisation des intervenants et des rebuts tout au long du projet.
- Installer les équipements de manutention aérienne.
- Installer les services électriques et d’air et les autres services requis jusqu’au point de raccordement ou près de ceux-ci.
- Nettoyer l’usine actuelle et se défaire de tout ce qui est inutile.
- Développer une planification détaillée des mouvements d’équipements et du matériel pour le déménagement. Organiser le tout dans un diagramme de Gantt.
- Mettre en place une équipe et désigner une personne responsable, les jours de déménagement, à la fois sur les lieux d’origine et à la destination.
- Vérifier régulièrement les travaux de préparation (murs, prises électriques, sorties d’air, etc.).
- Emballer et préparer le matériel pour l’expédition par les employés.
- Marquer le sol de l’usine pour déterminer l’emplacement des équipements et des postes de travail.
- Vider et déménager les étagères de matières.
- Monter les étagères à la destination.
- Replacer le matériel dans les étagères.
- Débrancher les équipements sur les lieux d’origine.
- Déménager les équipements.
- Déménager et installer les postes de travail dans l’usine et dans les bureaux.
- S’assurer de la pose d’étagères, de tablettes ou d’autres éléments sur les murs rapidement.
- Brancher tous les équipements et les postes de travail.
- Inspecter les installations pendant et après le déménagement.
- Essayer les machines et les procédés avant de lancer la production et obtenir l’approbation du contremaître pour chaque machine, une à la fois.
- Obtenir une approbation du bon fonctionnement global.
- Approuver les paiements et vérifier le respect du budget.
Règles d’un bon aménagement
- Il élimine ou réduit les activités à non-valeur ajoutée comme les déplacements et les manutentions inutiles.
- Il est sécuritaire et respecte la réglementation s’il y a lieu (CNESST, environnement, Régie du bâtiment pour les appareils sous pression, gicleurs, produits dangereux, etc.).
- Il privilégie le rapprochement des postes de travail consécutifs et un flux continu. Il faut donc faire attention et ne pas profiter du vaste espace disponible pour s’étaler et éparpiller les machines, postes de travail et espaces d’entreposage.
- Il tient compte des flux de production des principales familles de produits de l’entreprise (s’il y a lieu).
- Il prend en considération la localisation des différents services avant de penser à un aménagement spécifique des équipements à l’intérieur d’un même service.
- Il est flexible et on peut facilement le modifier de manière à répondre à de nouveaux besoins.
- Il est élaboré avec la participation des employés de production. Le fait de consulter le personnel et de permettre sa participation facilite généralement l’implantation d’un nouvel aménagement ou d’une nouvelle méthode de travail. En effet, les employés consultés vont plus facilement s’approprier le nouvel aménagement (ou la nouvelle méthode de travail) que ceux qui ne l’auraient pas été, et la résistance au changement sera réduite chez les premiers.
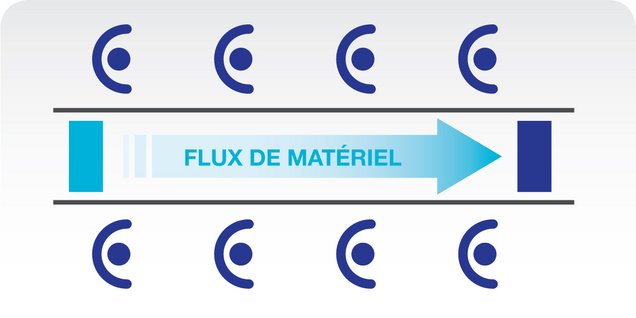
Exemples de conceptions inefficaces
Chaîne de production sur deux côtés
- Les opérateurs sont isolés à leur poste de travail.
- L’entraide est difficile.
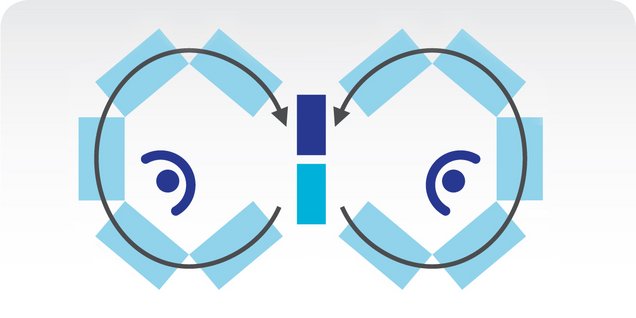
Cage d’oiseau
- Mêmes inconvénients que la chaîne de production sur deux côtés.
- Il est impossible d’augmenter la production.
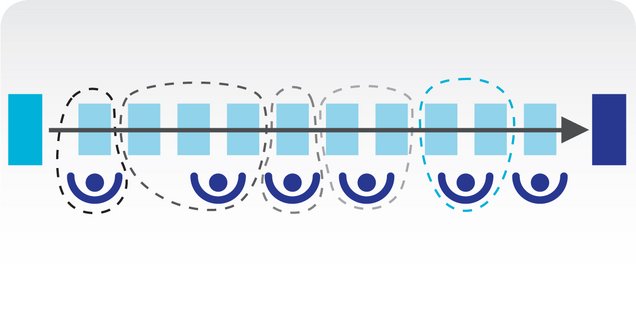
Chaîne de production sur un côté
- Il est difficile d’équilibrer le flux.
Aménagement cellulaire
L’aménagement cellulaire est un regroupement d’équipements ou de fonctions effectué selon les exigences technologiques des produits. Il a pour but de rendre la circulation plus fluide en diminuant :
- les distances;
- les surfaces utilisées;
- les temps d’attente.
Le principe de base sur lequel il repose consiste à tenir compte de la similitude entre les diverses opérations et le regroupement des produits du même type. On améliore la productivité en exécutant les opérations semblables et en standardisant les opérations ayant des liens entre elles.
L’aménagement cellulaire se présente généralement sous la forme de cellules en « U » afin de permettre aux opérateurs d’effectuer ou de surveiller plusieurs opérations à la fois. Il est particulièrement adapté lorsque l’entreprise dispose d’un grand nombre de familles de produits (une cellule par famille).
Dans le cas contraire, c’est-à-dire lorsque l’entreprise n’a qu’une seule famille de produits présentant peu de variations, un aménagement linéaire (avec flux continu et capacité équilibrée entre les postes de travail) est souvent plus avantageux.
Conditions préalables à l’aménagement d’une cellule de travail
- Le temps de mise en course doit être rapide.
- Les travailleurs possèdent l’habileté nécessaire pour équilibrer les opérations.
- La production se fait par familles de produits.
- Le volume est suffisant.
- Les travailleurs, dans la cellule de travail, ont les compétences et les connaissances requises pour effectuer toutes les tâches (formation croisée).
Caractéristiques de la cellule
- Elle dépend davantage de la main-d’œuvre que de l’équipement.
- Les travailleurs sont multifonctionnels.
- L’équipement est flexible et petit.
- L’espace utilisé est compact.
- Le transport des matières et des produits est réduit.
- Il y a absence de retours en arrière.
- Elle occasionne une diminution des produits en cours.
- L’ajustement de la capacité est rapide grâce à une répartition équilibrée du travail entre les travailleurs.
- Le temps de cycle est plus court.
Exemples de cellules de travail performantes en « U »
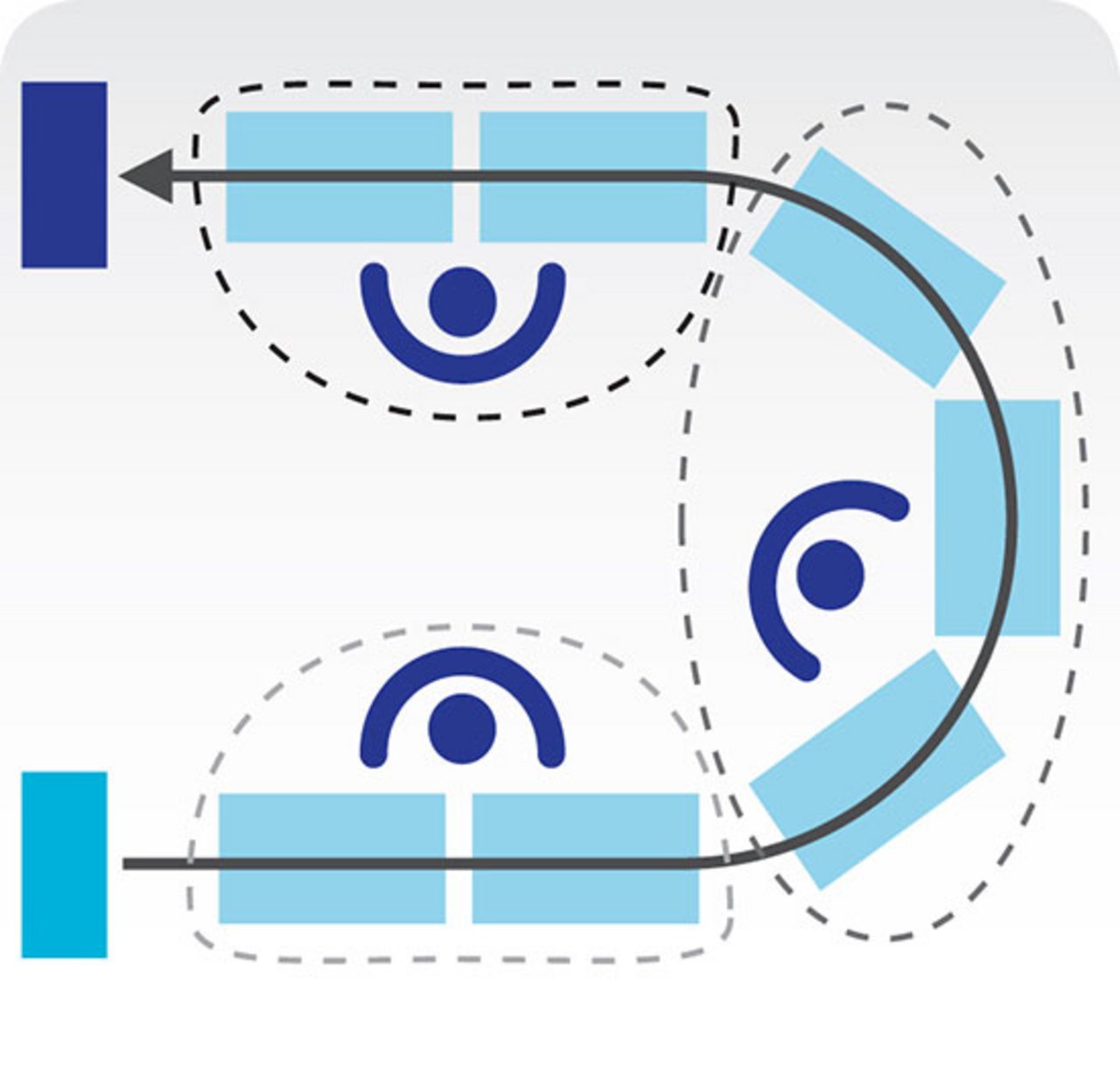
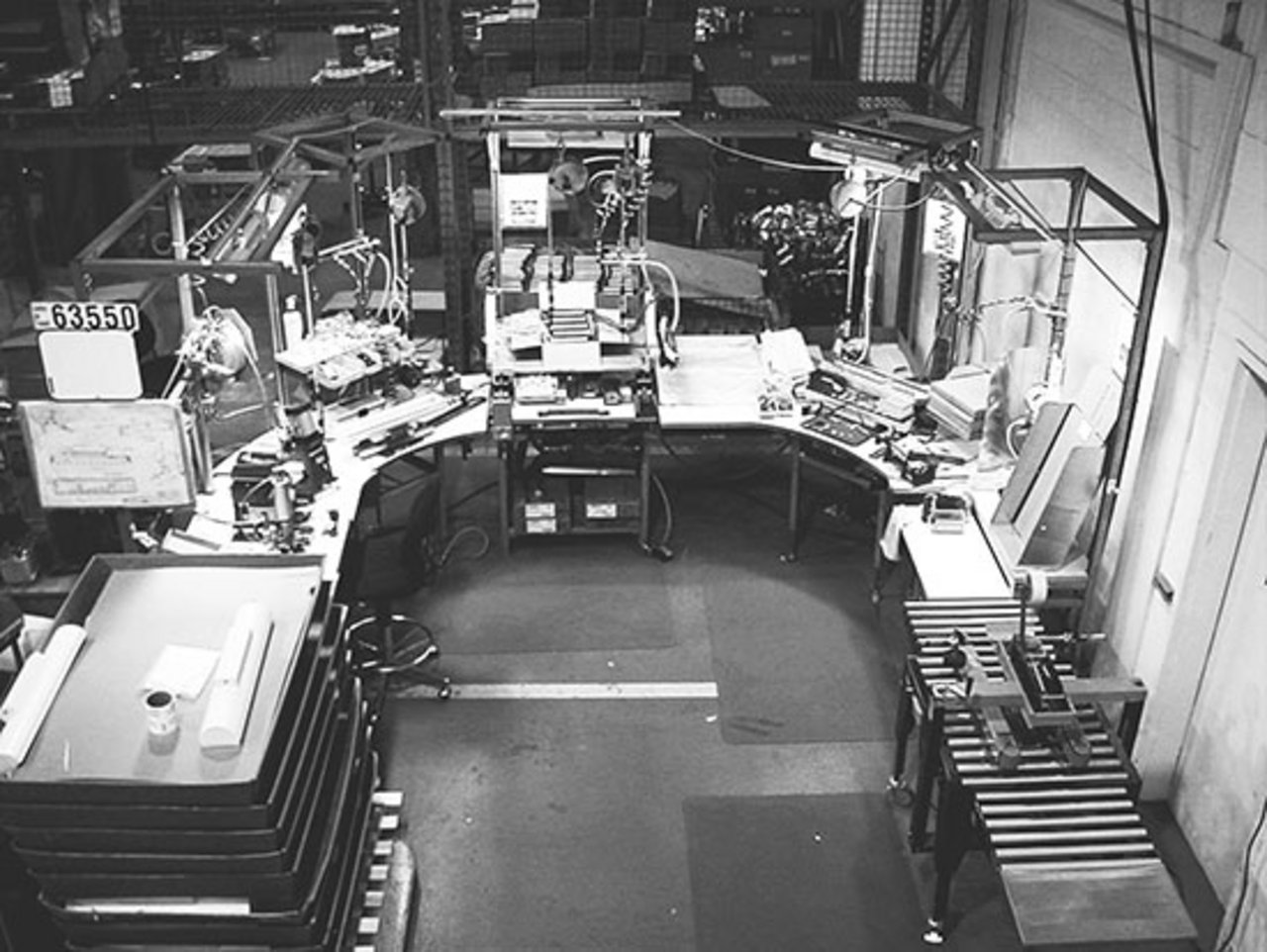
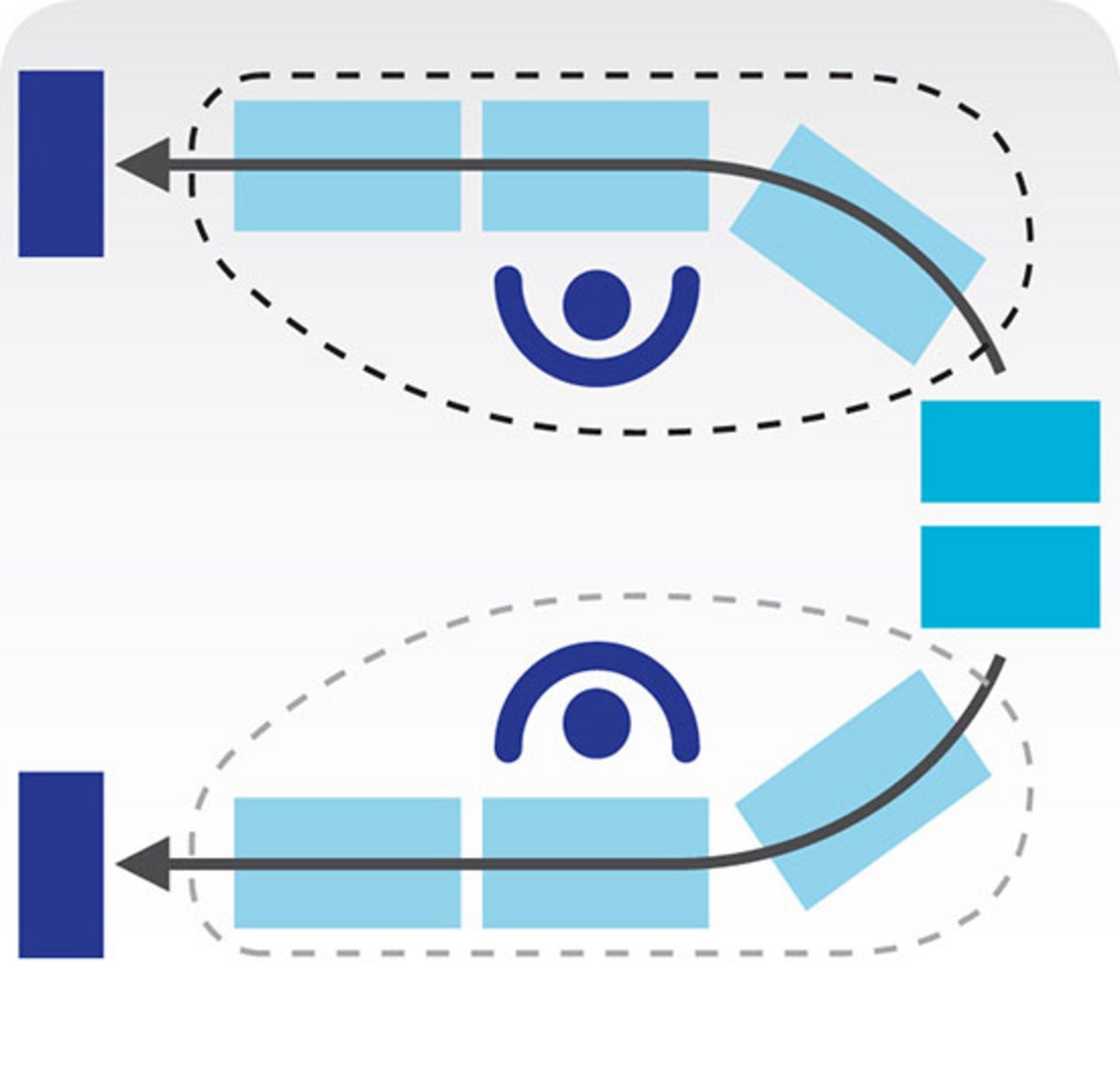
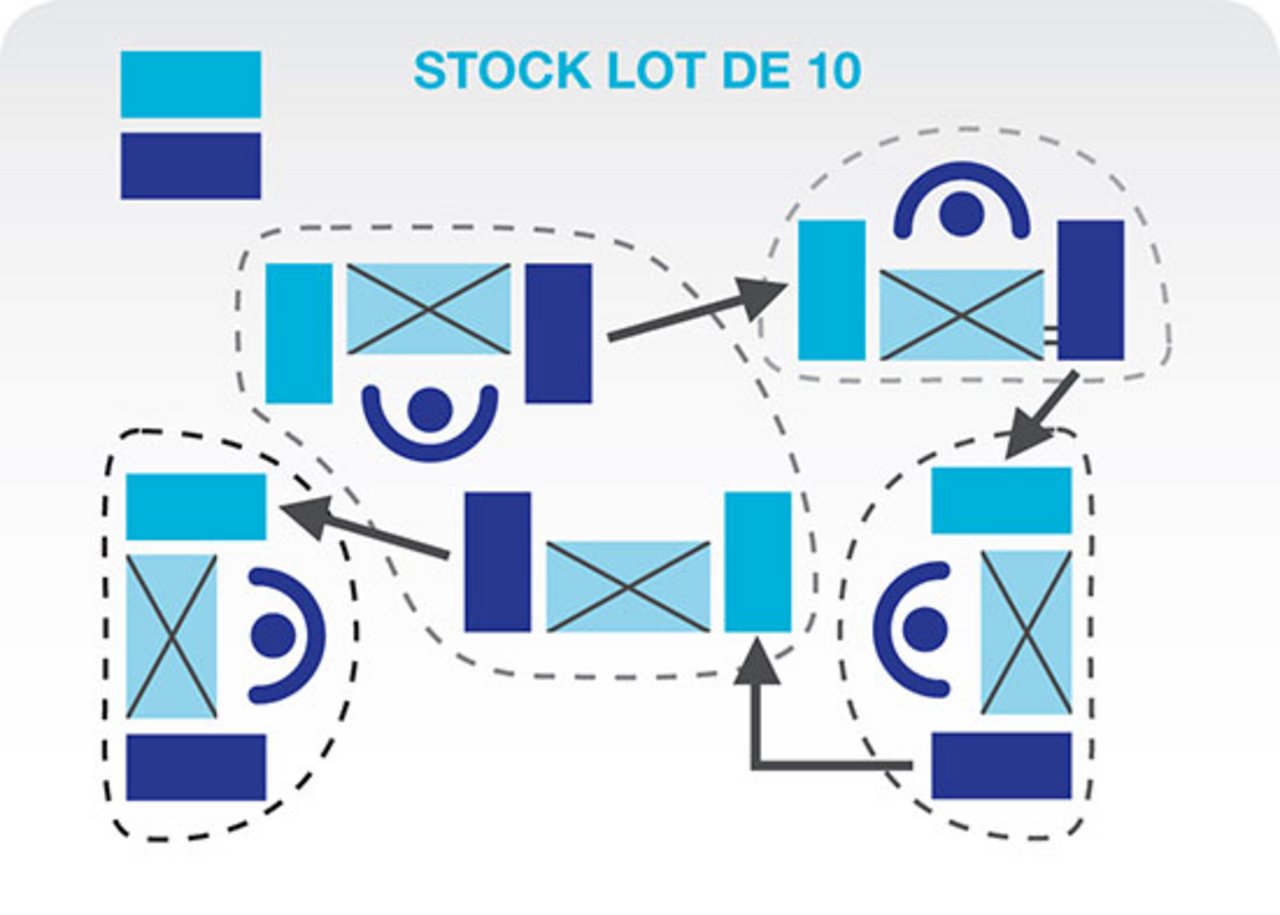
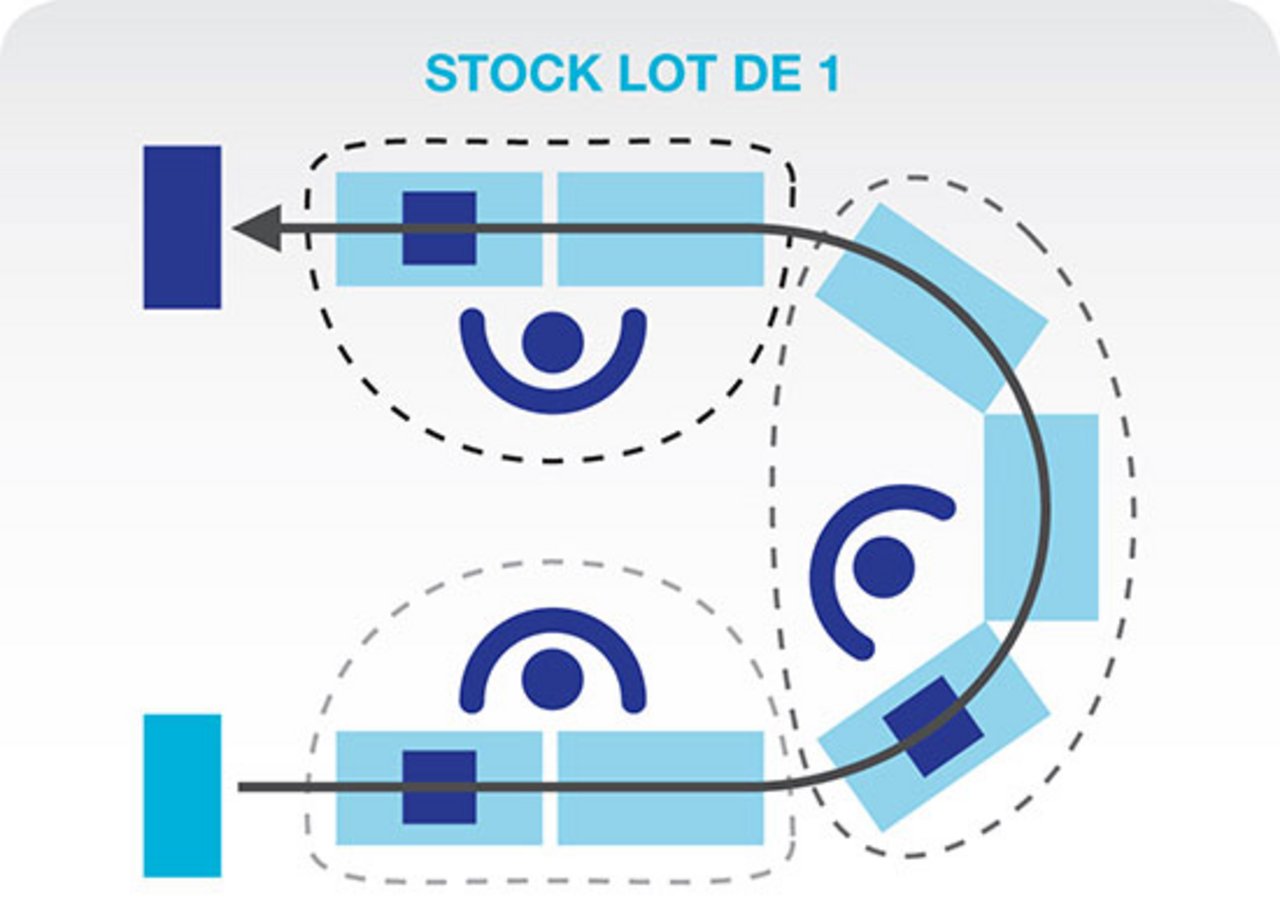
Flux continu et unitaire
Le flux continu et unitaire existe lorsque les produits ou les pièces se déplacent dans un procédé un à la fois, au rythme désiré par le client. Cette méthode permet :
- d’augmenter la vélocité des produits;
- de faciliter la gestion du processus;
- de réduire la quantité de matériel entre les postes de travail.
Bénéfices de l’optimisation des flux
- Réduction des délais de fabrication.
- Amélioration de la productivité.
- Visibilité et rétroaction immédiates entre les opérations.
- Qualité accrue
- Gain d’espace (de 30 % à 50 %).